Steel, an indispensable material for modern life, relies heavily on coal for its production – 70% of steel is produced using coal. Metallurgical coal, also known as coking coal, plays a crucial role in steel-making.
Steel Production
-
The first stage is to transform coking coal into metallurgical grade coke, which is almost pure carbon. The process begins with the crushing and washing of the coking coal. It is then ‘purified’ or ‘carbonised’ in a series of coke ovens, known as batteries, where it is heated to 1000-1100ºC in an oxygen-free environment for 12-36 hours. This process removes by-products and results in the production of coke.
-
The second stage is to produce ‘pig’ iron, where iron ore is reduced to iron, the precursor to steel production. A blast furnace is filled with iron ore, coke, and small quantities of fluxes (minerals used to collect impurities). Heated air (about 1200°C) is blown into the furnace through nozzles in the lower section. The air causes the coke to burn, producing carbon monoxide which reacts with the iron ore and heat to melt the iron. Finally, molten iron and slag (impurities) are drained off through a tap hole at the bottom of the furnace.
-
Steel is produced in several ways. The blast furnace-basic oxygen furnace (BF-BOF) route uses the pig iron which is then processed in a BOF where the carbon content of iron is adjusted, and additional metals are added to make different steel grades as follows:
- Carbon Steel: This is the most commonly used steel with low to high carbon content for structural and general applications. It contains only trace amounts of elements besides carbon and iron.
- Alloy Steel: This type of steel has added elements such as manganese, nickel, chromium, or silicon. These elements are used for improving strength, hardness, or corrosion resistance.
- Stainless Steel: This type of steel has a high chromium content and is used for its resistance to rust, stains, and corrosion. It may also contain nickel, silicon, manganese, and carbon.
- Tool Steel: This type of steel has a high carbon and alloy content. It makes cutting and drilling tools, knives, and dies.
- The properties of steel can be altered dramatically by adding different proportions of materials such as Chromium, Carbon, Manganese, Nickel, Molybdenum, Titanium, Silicon, Phosphorus, and Sulphur. Hardness, corrosion, oxidation strength, and the ability to weld are all affected by adding the above materials.
The Blast Furnace-Basic Oxygen Furnace (BF-BOF) route is responsible for more than 70% of global steel production, underscoring the significance of this coal-based method. The BF-BOF process involves reducing iron ore to molten iron in a blast furnace, which is refined into steel in a basic oxygen furnace. Given its dominance in steel production, advancements and improvements in this method can substantially impact the steel industry’s overall efficiency and environmental footprint. The increased use of scrap steel, recycling byproducts such as blast furnace slag for cement, and CCS are all being explored.
The Electric Arc Furnace (EAF) method accounts for 29% of global steel production. This process relies entirely on recycled scrap steel and requires substantial electricity. However, it’s important to note that a certain quantity of pig iron produced from blast furnaces is still necessary.
The limitations of each steelmaking process mean switching from one process to another is not straightforward. The BF-BOF route requires efforts to decarbonise the process, which may include greater raw material efficiency and CCS efforts.
The EAF process requires affordable electricity and scrap. Switching to electric-based systems needs affordable, reliable, decarbonised electricity, and reliance on renewable power may not deliver this in the quantities needed to replace the world’s BF-BOF.
Growing demand for steel is outpacing the release of scrap from the steel pool today. this means scrap recycling provides limited scope for growth in this sector. Scrap supplies require sophisticated and adequate capacity capacity to separate metals from other wastes. There is no easy way to dismantle and sort recycled materials when needed at the scale of the current world steel market. Similarly, hydrogen-based steel production, such as Hybrit, will require vast amounts of electricity to electrolyse water for H2 production.
Decarbonising the steel sector
Steel production is a carbon-intensive process, contributing significantly to global CO2 emissions. This is where Carbon Capture and Storage (CCS) comes into play. CCS is a technology that can capture up to 90% of the CO2 emissions produced from industrial processes like steel production. The captured CO2 is then transported and stored deep underground in geological formations. This makes CCS a key technology for reducing greenhouse gas emissions and combating climate change.
In the context of steel production, CCS can be particularly effective. For instance, the BF-BOF process, which accounts for 70% of today’s steel production, produces about 2.3 tonnes of CO2 per tonne of crude steel. Implementing CCS in this process can significantly reduce these emissions. However, despite the effectiveness of CCS, its implementation on a large scale in the steel industry has been limited. Financial incentives and regulatory frameworks have not been sufficient to spur multiple large-scale projects. This must change. But with increasing awareness and urgency to address climate change, the role of CCS in decarbonising the steel sector is expected to grow.
Building our Modern World
According to United Nations estimates, the global population is projected to increase from 8 billion to 10 billion by 2050 and further rise to 12.4 billion by the end of the century. Currently, urban dwellers comprise 55% of the total population, which is anticipated to climb to nearly 70% by mid-century.
This trend towards urbanisation and industrialisation is expected to fuel a robust demand for steel and cement, particularly in Asia, where coal is a critical resource for the majority of steel and cement production. Due to its versatility and wide range of applications in consumer goods, transportation, construction, and infrastructure, steel ranks as one of the most extensively utilised materials worldwide.
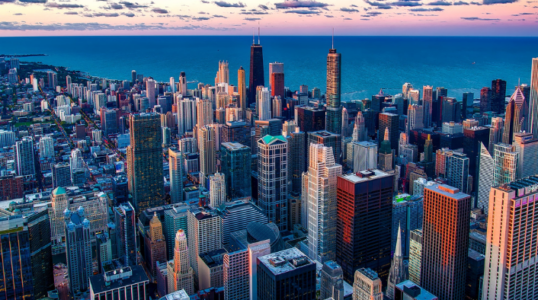
Using Steel to Build Renewables
Affordable steel is a crucial component in the production of equipment for renewable energy. This is particularly evident in China, which has established itself as a leader in manufacturing renewable energy technologies. According to the Global Energy Monitor, China has set ambitious targets to reach approximately 1,371 gigawatts of wind and solar capacity by 2025.
The production of each wind turbine requires a significant amount of steel, which in turn necessitates the use of coal. Specifically, manufacturing a single wind turbine involves using 170 tonnes of coking coal and 300 tonnes of iron ore.
China’s prominence in renewable energy and coal and steel manufacturing is expanding concurrently. The role of coal in this context extends beyond being a source of energy. It is instrumental in supporting the production of renewable energy technologies and ensuring grid stability.
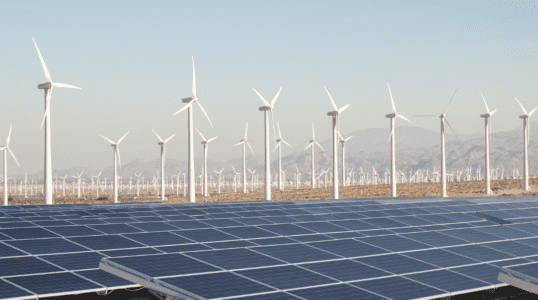
Going Forward
Looking towards the future, the World Steel Association projects a significant increase in steel usage. By 2050, it is estimated that the steel demand will grow by an additional 20%. This forecast underscores the enduring importance of coal, as it continues to be a crucial component in steel production and industrial growth.
The projected rise in steel demand is likely to be driven by various factors, including urbanisation, population growth, and industrial development. As economies expand and societies evolve, the need for infrastructure, transportation, and consumer goods – all of which rely heavily on steel – will increase.
Given that coal is a key ingredient in steel production, its role remains integral to the growth of this vital industry. Therefore, even as we strive for cleaner and more sustainable energy sources, the significance of coal in industrial processes such as steel production continues to be a critical consideration for the future.
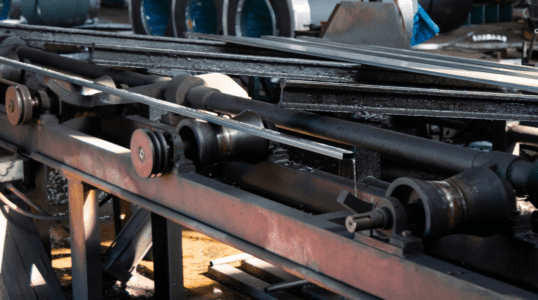